Vhodný koncept pro řízení výroby je bezpochyby závislý na typu či dispozičním uspořádání výroby. Jakou možnost výběru mají manažeři výrobních podniků v oblasti konceptů řízení výroby? V čem se tyto koncepty odlišují?
V oblasti systémů pokročilého plánování je terminologie stále ještě neustálená, nicméně zkratka APS (Advanced Planning System) slouží především pro označení podpory optimalizace na úrovni dílenského rozvrhování a SCM (Supply Chain Management) zahrnuje celý rámec plánovacího procesu dodavatelského řetězce.
Manažera výrobního podniku však zajímá především to, že konkurenceschopnost jeho výrobků závisí na ukazatelích jako je produktivita, kvalita produkce, kvalita poskytovaných služeb atd. Možnost ovlivnit tyto ukazatele má však manažer nejen během výrobní fáze, ale již v počátku volby vhodného konceptu pro řízení výroby. K metodám (resp. konceptům) řízení uplatňujících se v APS/SCM systémech, patří: Just In Time (JIT) a KANBAN, řešení typu Manufacturing Resource Planning (MRP II), Teorie omezení (TOC - Theory of Constraints) a Total Quality Management (TQM). Pochopení jejich podstaty, odlišností a výhod použití dobře dokresluje také uvedení jejich stručného vývoje a porovnání.
JIT a KANBAN
Metoda JIT má využití v zásadě ve dvojím pojetí. Modernější přístup ji charakterizuje nikoli jako systém vedoucí ke snížení zásob, ale jako systém, který vede k úspoře času v celé průběžné době výrobku. Druhé pojetí spočívá v použití JIT pro řízení jednotlivých stupňů výroby či mezi jednotlivými provozy. Obecně je pak možno jako JIT v případě jednotlivých pracovišť chápat i princip KANBAN. Ten je vhodným nástrojem pro dílenské řízení výrobního procesu a plánování výroby. Tato metoda se však rozšiřuje i do dodavatelských a odběratelských činností. Z pohledu řízení a plánování výroby se jedná o využití principu tahu (pull). Zákazníci svými aktivitami pak vyvolávají přímé reakce svého dodavatele. Tak se vytvoří samořídící regulační okruhy. Jednou z předností zmiňované metody jsou jednoduché pomůcky pro její aplikaci v podniku jako např.: tabule pořadí KANBANů, plánovací tabule, výrobní, dopravní, plánovací a signální KANBANy, světelné (zvukové) signalizační zařízení.
KANBANová tabule mezi střediskem Lisovna a Svařovna ve společnosti LINET, s.r.o.

Klikněte na obrázek pro zvětšení
Co je potřeba pro zavedení metody JIT?
- V oblasti pracovních sil: kvalifikovaný, vyškolený, ale hlavně motivovaný personál a připravenost delegovat pravomoci na každé úrovni řízení;
- Z hlediska typu výroby: opakovaná výroba stejných nebo příbuzných součástek s velkou rovnoměrností odbytu (hromadná a sériová výroba) s harmonizovanými kapacitami (tzn. zamezení vzniku úzkých míst);
- Rychlé seřizování strojů a zařízení, částečná pružnost kapacity (přesčasy) a plynulé toky (tzn. správně navržené rozmístnění kapacit na dílně);
- Rychlé odstranění poruch obsluhou zařízení a kontrola kvality přímo na pracovišti.
Co může JIT podniku přinést?
Jednoznačně snížení zásob, zvláště snížení mezioperačních zásob, které se omezí jen na bezpečnostní zásoby. Dále zajištění systémového toku informací v celém procesu výroby a dodávek dílů, založeného na sledování předem určeného stavu zásob, podporu plynulosti výroby při nárůstu sortimentu, zmenšení pracnosti plánování (tvorby plánu, kontroly), přehled o stavu výroby a zásob rozpracované výroby, úsporu přepravních nákladů a v neposlední řadě se jedná o jednoduchý, technicky nenáročný a flexibilní systém dílenského plánování, který je "otevřený" pro všechny pracovníky a výrobní týmy.
Softwarové produkty týkající se oblasti plánování a řízení výroby, respektive celého logistického toku zakázky se v devadesátých letech označovala (v německém prostředí) shodně zkratkou PPS (Produktionsplanung und -steuerung), která je analogií systémů MRPII (v anglosaských zemích). Řešení typu MRP II či PPS znamenala tedy největší změny v podnikových IS po roce 1990.
MRP
Původní systémy MRP (MRP jako Material Requirements Planning) prosazovaly jako racionalizační prvek systémy řízení zásob, které byly schopny určit bod objednávky a stanovit velikost dodávky. Od roku 1965 zaznamenaly rozšíření MRP systémy jako systémy pro zajištění přesné kontroly o plánování nákupu, ale ve vazbě na výrobu a odbyt. Impulsem pro výpočet potřeby kusů a materiálů podle kusovníků či norem spotřeby jsou jednotlivé výrobní zakázky. Na základě spotřeby poté dochází ke stanovení potřeby materiálu. Systém je tak schopen zajistit časovou i kvantitativní vazbu mezi nákupem a odběrem.
Jaký je předpoklad pro umístění systému MRP?
Struktura kusovníku nemůže znamenat pouze výstavbu výrobku, ale obsahuje i informace jak má být výrobek naplánován a vyroben, existence přesných dat pro výpočet spotřeby a potřeby a disciplína uživatelů zejména v tom, že jsou stanoveny realistické operativní plány výroby.
V čem jsou koncepty MRP výhodné?
Především v oblasti využití výrobních kapacit. Pomáhají totiž přiblížit požadavky na výrobní zdroje, kladené plánem výroby, skutečnému výrobnímu zdroji, který je k dispozici. Hlavní výhodou je nízká úroveň rozpracované výroby a výrobních zásob, dobrá znalost jednotlivých materiálových potřeb, možnost generování různých řešení hlavního plánu výroby a umožňuje sledovat skladbu průběžné doby výrobků.
V čem je naopak jejich nevýhoda?
Problémy metody spočívají v zajištění pružné změnové služby v konstrukci, shrnutí veškerých potřeb či definování doby výroby vyráběné součásti, nákupu dílů ad.
MRP II
Je inovací původního systému MRP a znamená Manufacturing Resource Planning tj. plánování zdrojů pro výrobu. MRP II je rozšířen o další funkce materiálového hospodářství, plánování denního množství, kontrolní systémy připravenosti materiálu a sledování kritických částí. Další aplikace rozšiřují systém o některé prvky operativního plánování výroby, plánování nákladů na výrobu apod.
Jaký je hlavní přínos konceptu MRP II?
Bezesporu propojení chodu výroby z hlavními oblastmi řízení podniku jako celku. Toto rychlé propojení marketingu, finančního řízení a výroby umožňuje aplikaci ryze podnikatelského pohledu na produkci firmy. Těžištěm MRP II je také plánování materiálových požadavků. Činnost systému začíná integrací všech zakázek a celkové poptávky. V dalších fázích se vše postupně upřesňuje a přizpůsobuje důležitým požadavkům a okolnostem. Tento systém částečně umožňuje simulace ve smyslu dopředného řešení problémů.
Paralelně s rozvojem řešení typu MRP II či PPS se rozvíjela i softwarová podpora úloh finančního řízení, zejména účetnictví. Spojením těchto dvou funkčních linií vznikla řešení označovaná jako ERP (Enterprise Resource Planning).
Úspěšné řešení každého ERP projektu vyžaduje soulad ve strategii, cílech, postupu a dalších důležitých faktorech mezi zákazníkem a dodavatelem. Nároky jsou tedy podobné jako při zavedení konceptu TQM, kde až spojení úsilí celé firmy umožní jeho faktické uskutečnění.
TQM
Metoda TQM směřuje ke zvyšování produktivity za současného zvyšování jakosti a snižování ztrát z nejakostní výroby a zvyšování spokojenosti zákazníků. TQM je tedy systematické a důsledné uplatňování několika metod v rámci podnikové struktury, jasně zaměřené na jakost a spokojenost zákazníků.
Co je cílem TQM?
Obecně jde o to uspokojit zákaznické požadavky, a to co nejefektivněji. Zásadní podmínkou pro úspěch tohoto úsilí je aktivní účast všech zaměstnanců a to od recepce přes administrativu, výrobu, servis, obchod až ke generálnímu řediteli.
Je důležité měření kvality procesu?
Téměř všechny podniky dnes zavádějí programy jakosti. Základem každého z nich však je dokázat změřit kvalitu procesu tzn. soustředit se na: míru závad, úspěšnost (poměr počtu vyhovujících jednotek vystupujících z výrobního procesu k počtu jednotek do procesu vstupujících), odpad, odřezky, přepracování, vrácené výrobky, procento procesů pod statistickou kontrolou.
Jak je to u společností poskytujících služby?
Nejen výrobní společnosti, ale zejména firmy poskytující služby by měly hledat ve svých interních procesech chyby, které by mohly výrazně ovlivňovat náklady, dobu odezvy nebo spokojenost zákazníka. Požadovaným měřítkem kvality je v tomto případě počet průchodů zakázek v prvním kole obchodního procesu.
Koncept TQM se snaží docílit zvýšení kvality všech prvků. Ve srovnání s tím např. metoda TOC slouží jako periskop, který zaměřuje prvky, jejichž zlepšení přinese zvýšení kvality celého systému nebo jeho rozhodujících vlastností.
TOC
Principy metody TOC se rozšířily na poli softwarových řešení pod označením OPT (Optimized Production Technology). Metoda OPT se nesoustřeďuje jen na problémy výroby, ale i na ostatní činnosti v podniku. Metodu TOC lze aplikovat na libovolný typ systémů, ať už se jedná o výrobní firmu, obchodní společnosti, banky či pojišťovny.
Na co se TOC zaměřuje?
Primárně je orientovaná na úzká místa ve výrobních systémech. Představuje nový, netradiční způsob řešení problémů a způsob myšlení, který posiluje význam a úlohu zdravého rozumu. TOC v oblasti řízení výroby vychází z dat, potřebných též pro koncept MRP II, což je pouze částečně zřetelné u JIT a TQM. Protože TOC se zaměřuje na úzká místa, klesá do určité míry požadavek na přesnost dat, týkajících se ostatních prvků systému.
Metoda TOC se snaží o maximalizaci průtoků úzkým místem. Zásady TOC resp. postup jak pracovat s omezením je možné definovat v pěti bodech tak, jak uvádí dr. Goldratt: "Najděte omezení (úzké místo), rozhodněte jak omezení maximálně využít, vše ostatní podřiďte předešlému rozhodnutí, rozšiřte omezení a poslední bod znamená návrat na začátek."
Proč je TOC důležitá?
TOC je obecná manažerská filozofie a zároveň velmi účinný nástroj zaměřený na růst podniku a zvyšování dosahovaných hodnot podnikového cíle. Šíře jeho uplatnění je značná a zasahuje všechny důležité podnikové oblasti. TOC se uplatňuje především v těchto třech oblastech:
- Důležité podnikové funkce: výroba, distribuce, marketing, prodej či řízení projektů;
- Průtoková analýza: TOC může pomoci při změně rozhodování postavené na zohlednění nákladů k procesu trvalého zlepšování;
- Logistický proces v TOC představuje třetí úroveň všeobecně použitelných nástrojů pro identifikaci a řešení různých problémů v organizaci.
TOC manažerům napomáhá ale i v takových oblastech jako jsou vizualizace a zlepšení procesů ve firmě, řešení problému komunikace či pomoc při hledání nových přístupů s jejich následnou realizací.
Doporučujeme pragmatický přístup
Domníváme se, že v rámci podniku by mělo podle potřeby pracovat více (i odlišných) metod dílenského řízení. Na dílenské úrovni pak bude využitý ten koncept řízení, který bude pro daný typ výroby a výrobní systém nejvhodnější. Při volbě výše uvedených konceptů hrají roli kromě typu výroby a dispozičního uspořádání výroby roli i ukazatele jako např.: princip organizace výroby, struktura výroby, stálost odbytu nebo počty variant produktů.
Každá z metod dílenského řízení (resp. rozvrhování) je vhodná pro určité výrobní podmínky a každé zjednodušení bez upřesnění zmiňovaných ukazatelů je chybné. Zjednodušený přehled charakteristik řízení pro různé typy výrob a doporučené strategie pro dílenské řízení uvádíme v tomto schématu:
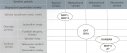
Klikněte na obrázek pro zvětšení
Článek byl publikován v časopise Connect! 7-8/2003.
21.08.2003 - David Tuček, Zuzana Holočiová - četlo 28936 čtenářů.